Award Details
Customer: Buell Motorcycle Co. East Troy, WI
Material: Magnesium
Alloy: AM60
Process: High Presssure Die Cast
Weight of Casting: 2.67 lbs.
Dimensions: 28” x 10½” x 7”
End Market: Recreational Vehicles
Challenge
Replace a costly 4 lb. aluminum weldment, consisting of many individual pieces, with a lightweight magnesium die casting.
Elements of the Challenge:
- Customer desired a one-piece solution.
- Reduce or eliminate secondary machining (weldment required significant milling, tapping and drilling at awkward angles).
- Accomodate all attachment points. Since numerous components mount to tail section on the upper and lower sides and the ends, reproducing all of these made parting line design a challenge.
- Filling the new casting required propagating metal through a rib lattice, along a 28” length, with important mounting detail at both ends and tall thin features in between.
Cosmetic Constraints The ribbed portion of the casting was exposed to showcase the new tail section design to retail customers, which limited gating and venting options if extensive handwork was to be avoided.
Distortion Risk With large slides opening in a way that could pull the casting apart, distortion was a significant risk.
Solution
After initial consultations, TCDC supplied the customer with a 3D model proposal for a one-piece die-casting. Based on the proposal, Buell revised their design to meet detail functional and aesthetic needs. The resulting product was a one piece die casting, with a price reduction of 70%. No secondary machining was required (just insertion of 5 rivet-like threaded inserts). The part weight was reduced by one third, even though its size increased significantly for the new model year.
Product Application Images
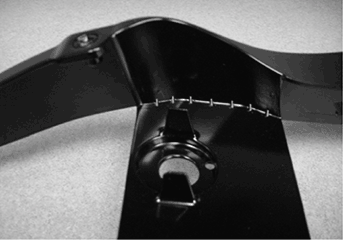
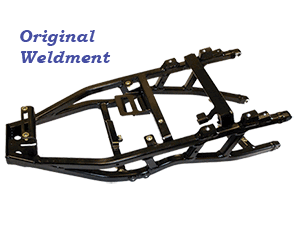