Tooling
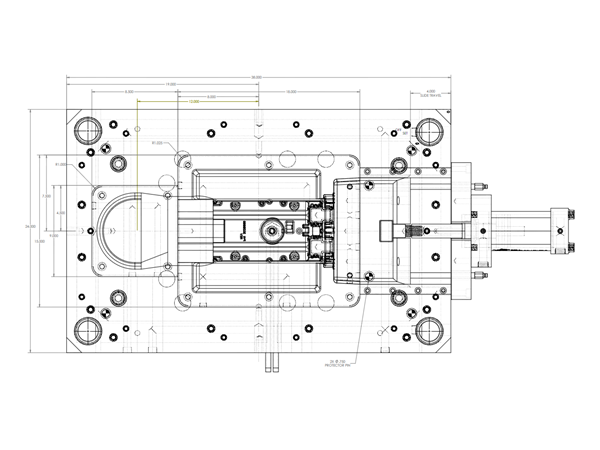
TCDC has a reputation for innovative tooling solutions. We design and run multiple-cavity die cast dies, and are willing to undertake more complex shapes than our competitors. Our domestic and global die cast tooling partnerships allow us to satisfy our customers; whether cost, tool life, or timing is the most important factor in purchasing tooling.
Dies, or die cast molds, are made from alloy tool steel in at least two sections: the fixed die half (cover half), and the ejector die half. When the die casting machine closes, the two die halves are locked and held together by the machine’s hydraulic pressure. During the die casting process, molten metal is injected at high velocity into the mold (die) cavity to form a die cast part.
Cast tooling is maintained to ensure optimal quality and maximum tool life. The exact life of die cast tooling depends on part geometry and complexity, required tolerances, and most importantly – the type of metal cast. In general, Aluminum tooling can last approximately 100,000 shots, while Magnesium tooling lasts 200,000 – 300,000 shots.
Tooling Configurations Examples:
There are a variety of tooling configurations to consider based on your desired output, including:
Single Cavity Tool: Produces a single casting.
Multiple Cavity Tool: Produces multiple parts at once.
Family Tool: Multiple cavity tool that produces multiple part numbers.